Why Getting Out of the Office is Our Secret to Better Software
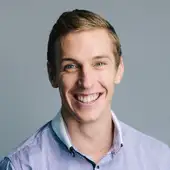
I'm a firm believer that great warehouse management software isn't built in isolation. That's why I recently packed up one of our talented engineering squads (teams) and hit the road, visiting customers in Sydney and Auckland to see our latest e-commerce features in action.
The Value of Customer Immersion
Software is developed in small independent chunks, each potentially requiring days, weeks or in some cases even months of design, development and testing. Going on site and seeing customers use all of these pieces together in a single seamless workflow is truly transformative for understanding the full value unlocked by thousands of individual small decisions throughout the development process.
This is exactly what happened when our team - Jane Dyachenko, Viet Vo, Ricky Camongol, Gabriela Sales, and Cody Ayson - stepped onto the warehouse floors of Motive 3PL (3PL warehouse) and Dicker Data (hardware distributors) in Sydney, followed by Flo & Frankie (fashion and e-commerce) and Chemcare (hazardous goods warehousing, storage and distributors) in Auckland.
These visits weren't about us showcasing new features to our customers – they were about us seeing firsthand how our solutions integrate into the unique workflows of each business. For our developers, especially, these experiences offer insights that simply can't be replicated in our office environment. (Check out the CartonCloud Warehouse we built in-office to test workflows in a warehouse environment here!)
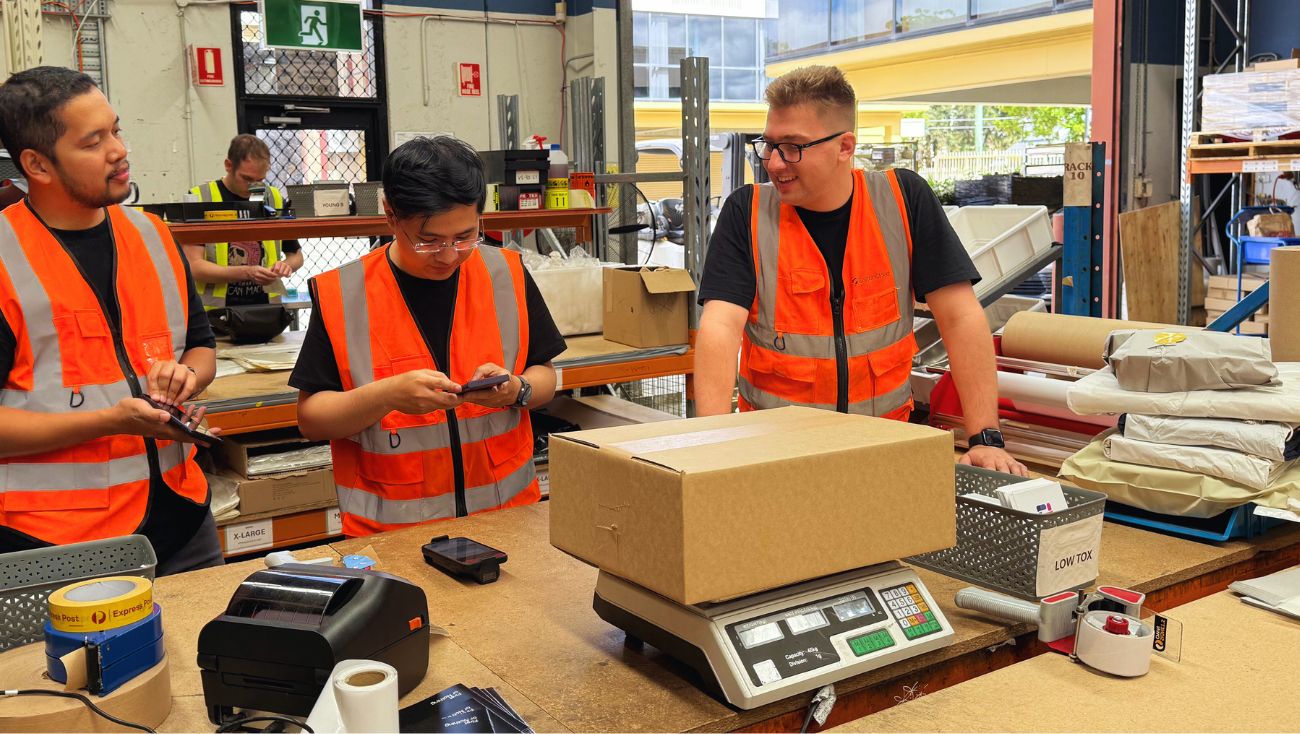
Seeing Our Latest E-Commerce Innovations in Action
Over the past six months, our team has been laser-focused on enhancing our software’s e-commerce capabilities. Three key features took center stage during our visits:
Pick to Tote
Watching warehouse staff at Motive 3PL, Flo & Frankie and Chemcare navigate through their picking processes using our Pick to Tote functionality was particularly enlightening. Pick to Tote was released in January, and allows pickers to efficiently batch multi-item orders together into waves which can be picked with reduced walking time. In addition to validating all the hard work our team put into developing this capability, by closely watching how both our team, and our customers used Pick to Tote, we uncovered several minor improvements that could be implemented to save even more time. *Check out our monthly New Feature RoundUp blogs and Release Log to stay on top of improvements and feature updates.
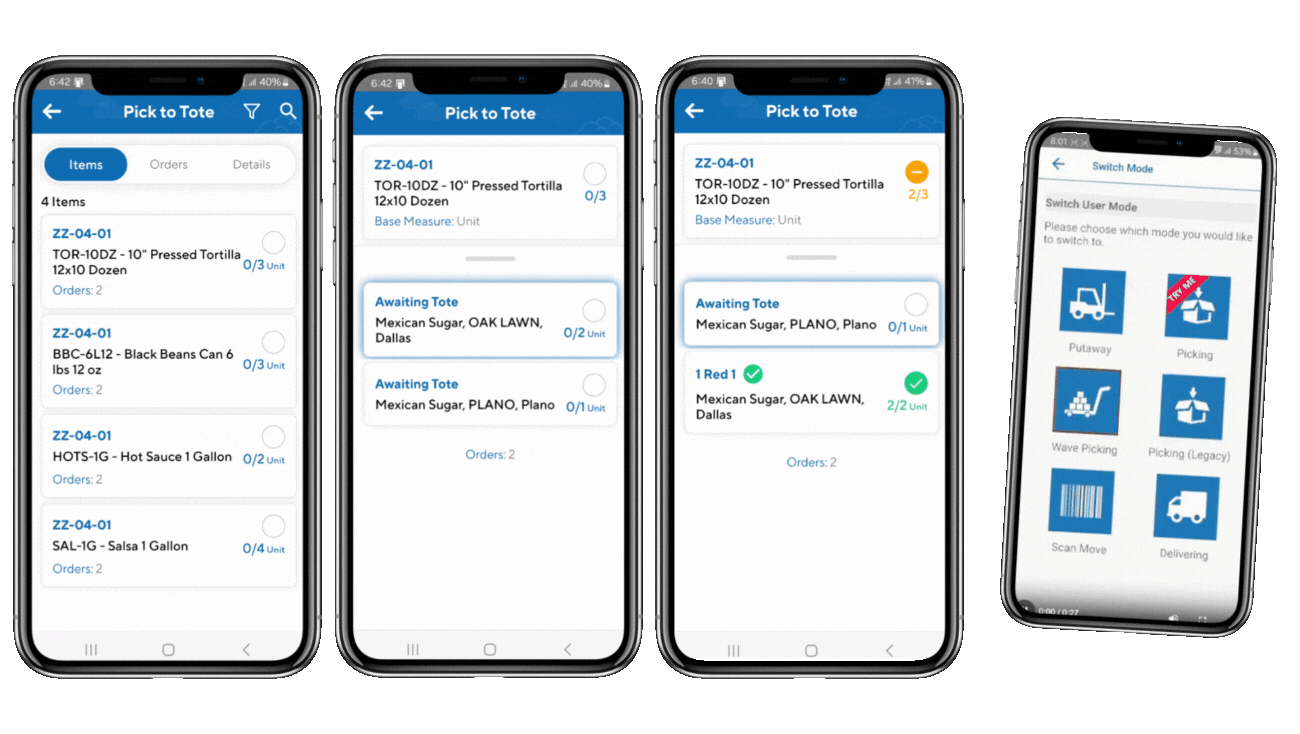
Pack by SKU
At Flo & Frankie & Motive 3PL, we saw first-hand how our Pack by SKU feature (released November 2024) had transformed their fulfillment process. Rather than the traditional method of packing one order at a time, searching for the right product to pack on a trolley of items, their team could now simply scan any item and have the system jump to an order requiring that product. For single-item orders, the efficiency gains were immediately apparent – zero time spent searching for items, and ultimately, faster order fulfillment.
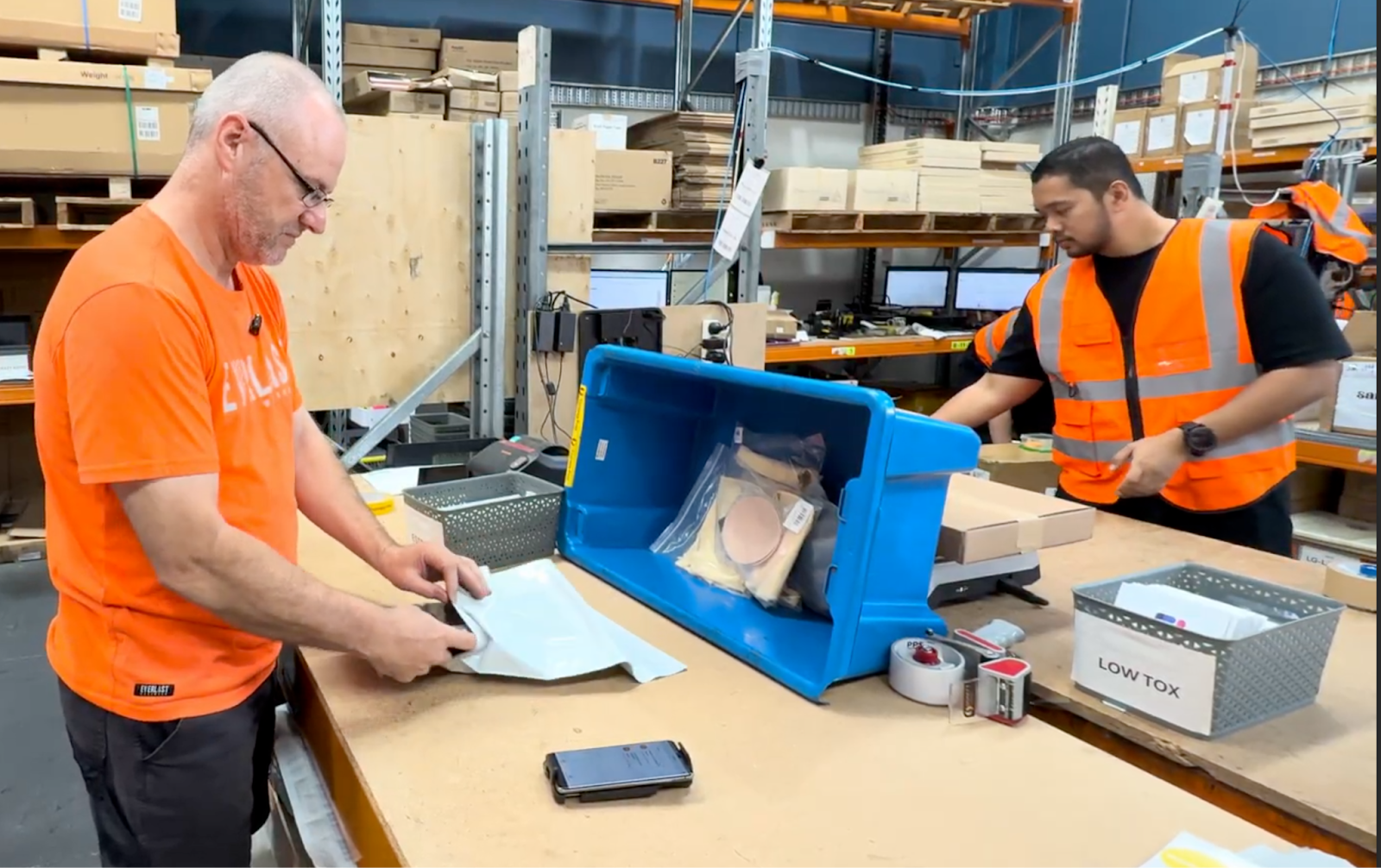
Enhanced Wave Picking
The enhancements we've made to our Wave Picking functionality over the last six months were put to the test at all four sites. The additional filtering options and template-based autogeneration capabilities we have released over the last 6 months have enabled our customers to create significantly more optimised waves. Watching pickers move through the warehouse with newfound efficiency was incredibly rewarding. The improved throughput spoke volumes about the impact of these improvements.
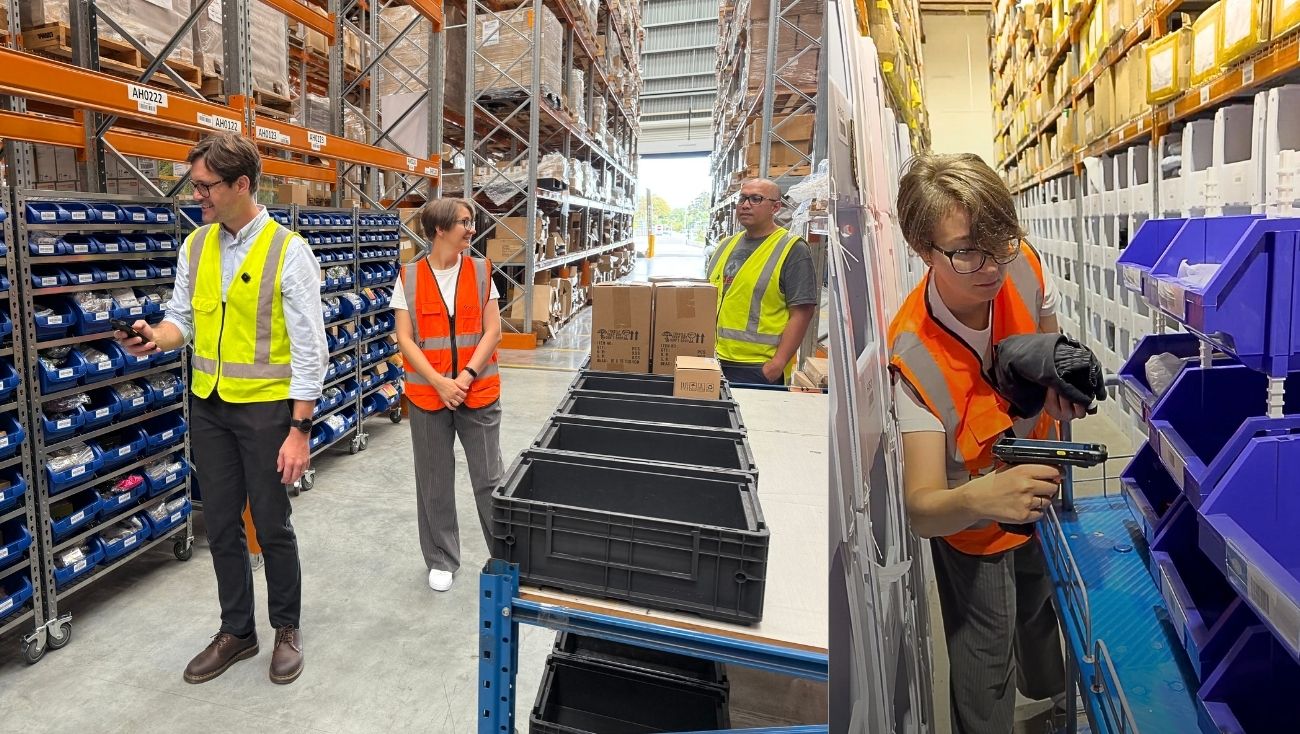
The Power of Partnership: From Feedback to Features
What makes these visits so valuable is the unfiltered, real-time feedback we receive. At Motive 3PL, a team member suggested a minor UI adjustment that would save seconds on each order – something our team might never have considered without this direct interaction. At Dicker Data, we observed unique challenges related to their high-volume operation that prompted immediate discussions about potential optimisations.
These customer visits reinforce what I've always believed: great software development isn't just about writing good code; it's about creating solutions that solve real problems for real people. For our developers, these experiences transform abstract user stories into tangible human needs. Jane Dyachenko, one of our senior developers based in Auckland, mentioned how using Pick to Tote to pick an entire wave at Flo & Frankie gave her a new perspective on the impact of her work.
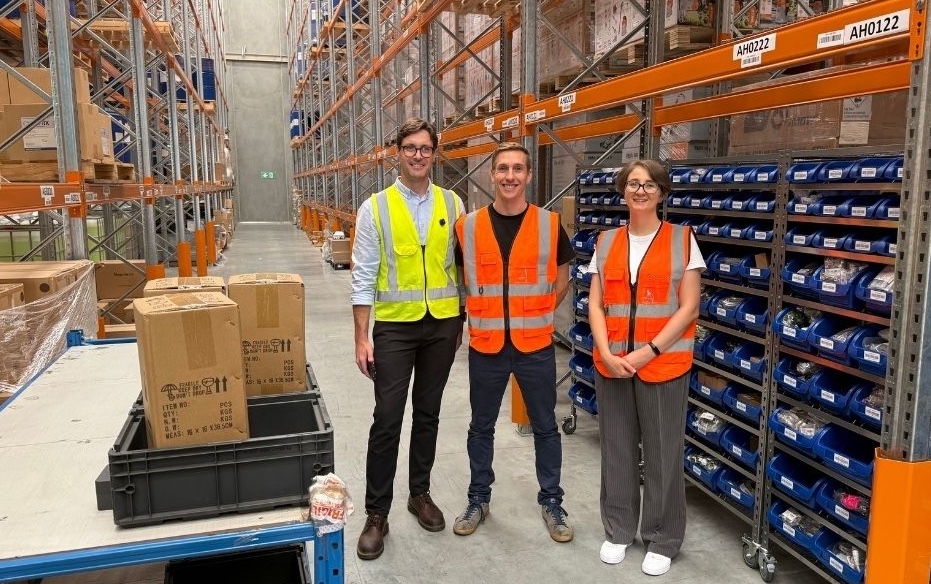
The feedback we received, particularly regarding our mobile application, has already resulted in tangible improvements. The insights have directly influenced a substantial number of time-saving enhancements introduced in our mobile app version 6.19.0 (released April 14th) and the upcoming 6.20.0 (scheduled for April 28th). These updates focus on streamlining workflows and reducing the number of taps required for common tasks – small changes that add up to significant time savings across thousands of daily interactions.
As we flew back to our headquarters in the Gold Coast, our team was buzzing with ideas inspired by watching our customers work. To Motive 3PL, Dicker Data, Flo & Frankie, and Chemcare – thank you for opening your doors and sharing your operations with us. Your partnership enables CartonCloud to build software that truly transforms warehouse management.
In an industry where efficiency gains of just a few percentage points can represent massive operational savings, understanding the nuances of each customer's environment is critical. We'll continue prioritising these visits because we know the best software solutions aren't built behind closed doors – they're developed in partnership with the very people who use them every day.
If you're interested in learning more about our e-commerce fulfillment solutions, including Pick to Tote, Pack by SKU, and our enhanced Wave Picking capabilities, visit cartoncloud.com or contact our team for a personalized demonstration.
Subscribe to CartonCloud
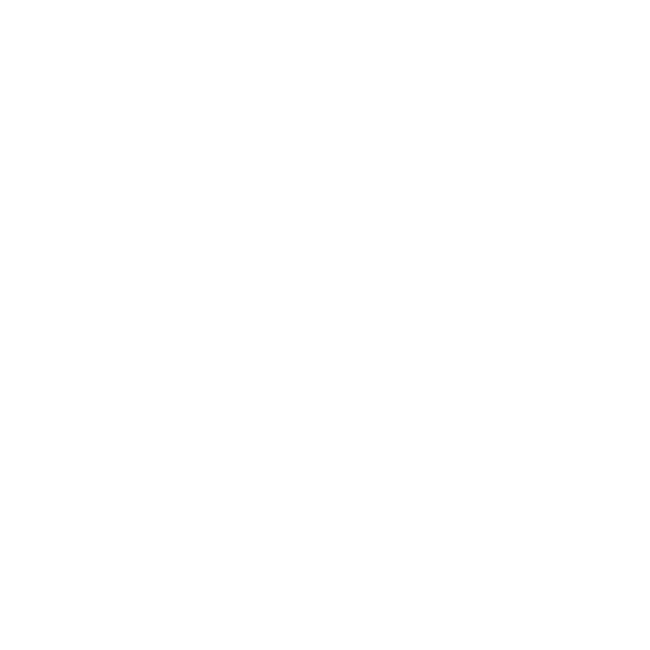