Top 5 ways to increase your warehouse ROI
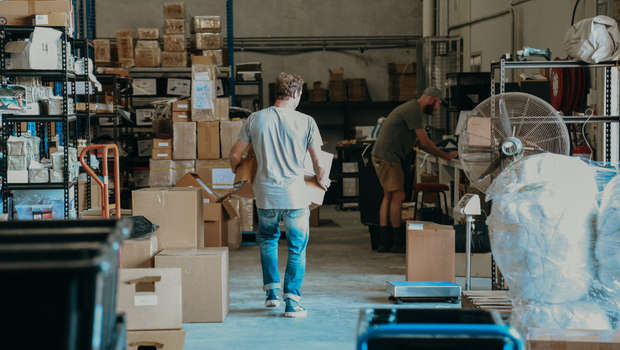
The magic words: increasing warehouse return on investment! With the right warehouse systems in place, increasing your warehouse ROI can be simple. Find out how to increase warehouse order output, and reduce overhead expenses by working smarter, not harder.
Let’s take a look at the top ways to increase your warehouse ROI with the right warehouse software system.
Warehouse software can not only increase efficiency and boost worker productivity, but the right WMS software also allows your team to increase daily order fulfillment while simplifying reporting and invoicing.
Cloud-based warehouse management software like CartonCloud can bring significant benefits to a small business warehouse, reducing your bottom line and allowing you to do more with the resources you have on hand.
Warehouse ROI is based on working efficiently and having the right systems in place to capture and check data — which are just two of the ways CartonCloud’s powerful WMS can help you grow your business.
How to increase your warehouse ROI in 5 steps
This countdown outlines the top five things you can do to increase warehouse ROI in your operations today.
5. Use warehouse locations
The layout of your warehouse can make a huge impact on productivity, speed of order fulfillment, and how to optimize storage rates.
Depending on the goods you store and the services your warehouse offers, there are different ways to optimize your space. This mainly comes down to allocating storage locations for accurate identification and optimizing storage by how often or how soon the goods will be needed.
Identifying warehouse locations with WMS software
Using cloud-based warehouse software, you can easily scale your operations up as needed, meaning you can accommodate changes in seasonal order volumes or in response to various customer needs. You can load warehouse locations into your WMS to allow your team to allocate a location for putaway, and easily identify the correct location when picking.
Optimizing warehouse locations for inventory pick and put-away
Next, you can start to strategically use the various storage location in your warehouse, to streamline picking and putaway activity; minimizing stock movement, and simplifying access for fast and accurate order picking.
To start with, you might want to store goods by batch; First in, First out (FIFO), or First Expired, First Out (FEFO), by temperature zone, or by using Replenishment to store fast-moving goods in easy-to-access locations. Each of these workflows can be implemented through your WMS, for the most accurate and streamlined workflow and setup.
Fast-moving items should be stored in the front of warehouse, in easy-to-access racking, or within pick faces located at the packing station for faster order fulfillment. For a sale item, free giveaway, or other frequently ordered goods, you can also take advantage of additional WMS features like Replenishment, which identifies when high-frequency items should be moved into a pick face.
4. Boost accuracy using barcode scanning
Another key area to increase warehouse return on investment is to use barcode scanning to ensure picking accuracy! For the best results in paperless pick and pack, we recommend using barcode labels to identify warehouse locations and confirm the items being picked.
Once your warehouse locations are set up in your WMS, you can use easily and accurately identify the physical spaces by simply scanning the location barcode with a mobile device or by pairing the mobile app on your smartphone to a Bluetooth barcode scanner.
Warehouse location barcodes can be used to assign a location during item put-away, or to confirm the correct location for order picking.
Why use barcode scanning? Scanning your locations and inventory for warehouse put away and picking means you have an added layer of certainty at each step, reducing mistakes and increasing your ROI.
For example, if you scan an incorrect location for pick or put away, or scan an incorrect item whilst picking an order, the CartonCloud WMS mobile app will show an error notification with vibration and sound feedback, to ensure you know there has been a mistake and can select the correct location or item. It provides a safety net, where mistakes are rectified at the moment, increasing your daily accuracy and ensuring smoother warehouse operations.
Want to know more about barcodes in your warehouse? Check out our article on everything you need to know about warehouse barcode scanning.
3. Automate your rates and invoices
If you can reduce or remove manual data entry and calculation; you should. By simply automating invoicing and rate card calculations, we’ve helped customers to save 80% on overheads, reducing admin hours by 40-60 hours a week, while actually increasing their daily output (see Liquex Logistic's story below!).
Capture all billable charges
Using a WMS with automated rate calculations also allows you to set complex rate cards for various customers, services, seasons, or other factors — ensuring you capture all billable charges and remove revenue leakage.
2. Ensure all inventory records are up to date, with a cloud WMS
Using a cloud-based WMS and mobile app to capture, record and track incoming orders, stock movement records and outgoing orders is essential in ensuring accuracy, simplifying reporting, and having the correct data for planning.
The benefits of a cloud-based WMS lie in the ability to capture data and update records from multiple sources, at the same time.
- Accept incoming orders from multiple sources with ease and accuracy; including online storefronts, customer emails, or manual order entry
- Allocate orders for picking and track orders as they progress
- Update stock reports throughout the day, including incoming and outgoing stock updates
- Calculate rates on the go, as stock is accepted, moved, and picked
- Provide customers 24/7 access to up-to-date reports from their own customer dashboard (without you lifting a finger).
When looking at increasing warehouse return on investment, the more you can save time, optimize processes, and simplify workflows — the more you can achieve in a day, and the greater ability you have to scale up your business.
Using a cloud-based WMS allows you to reduce manual data entry, increase accuracy, and automatically update your records across all touch points — giving you more control, more accurate data and picking, and more time to grow.
1. Integrate your WMS/TMS software for seamless data flow
Our final tip for increasing warehouse ROI is to optimize how information flows in and out of your warehouse, and across other areas of the supply chain.
Having a fully integrated cloud-based WMS and TMS gives you an enormous boost in terms of efficiently sharing data and optimizing workflows around order acceptance and dispatch.
- Immediately generate and attach a TMS delivery label to orders as they are packed in the warehouse to simplify dispatch, order tracking, and invoicing.
- Streamline cross-docking with oversight of incoming and outgoing orders, using barcode scanning to accept stock, sort, and allocate to a new delivery run — all from the palm of your hand, and directly from the dock.
- Optimize your processes beyond the warehouse by using delivery addresses and routes to pick and pack orders based on delivery routes.
- Capture order dispatch collection details with sign-on-glass for couriers as they collect outgoing orders from the dock.
No logistics company operates in a vacuum, and having a cloud-based WMS and TMS gives you the opportunity to connect, streamline and optimize operations both in-house and to align with your partners further along the chain.
These steps to increase your warehouse ROI will save you time, increase accuracy to save you money, allow you to increase daily order fulfillment, and improve your customer service — all allowing you to do more, with less.
Want to know more?
To find out more about increasing your return on investment for your warehouse operations, speak to our experienced team today.
We’re logistics people too, which means our team understands your business and can provide expert advice to support you throughout your business growth.
Subscribe to CartonCloud
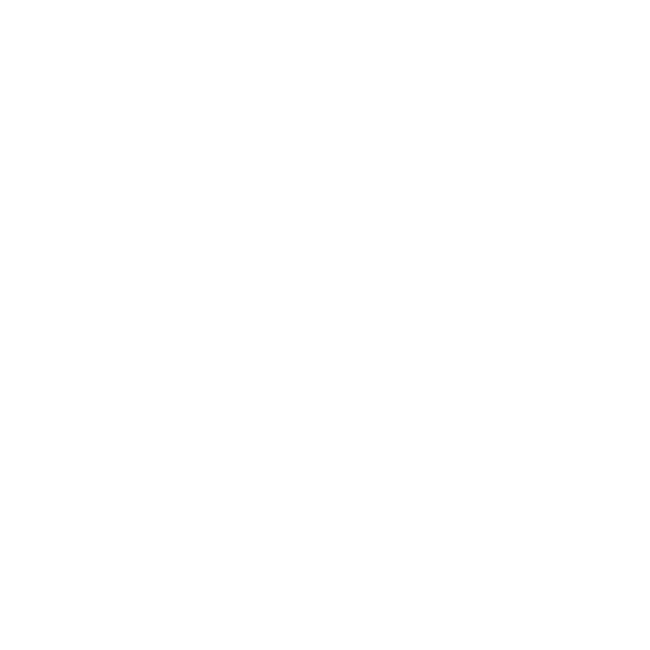