October 2024 — New Feature Monthly Round Up
Welcome to CartonCloud’s October 2024 New Feature Roundup! This month, we’re thrilled to introduce our Pick to Tote beta release, expanded Wave Pick functionality, enhanced Warehouse Location editing, and significant updates to Photos & Documents on Purchase Orders. Discover how these new features can optimise your warehouse operations!
October 2024 New Features:
- 🛒 Pick to Tote [*Beta]
- 🤳Wave Pick Templates & Wave Pick Auto Generation [*Beta]
- —*Join the Beta release user groups today!
- 📸Photos & Documents on Purchase Orders Improvements
- —Document Creation from Product View
- —New Video Support
- —New Lightbox Feature
- —Grid View Layout Option
- —Photos and Documents Academy Trail
- 📍Editing & Emptying Warehouse Locations
- 🙋🏽CartonCloud Survey Launch
And, stay tuned for these exciting new features coming soon!
- Mobile-based Wave Pick Generation
- Photos & Documents on Sale Orders
- Replenishment Auto Generation
- Pack Screen
- API Enhancements
- —TMS Quote API
- —Consignment Update API
- —Invoice Webhook
- Consignment-Item Scanning (TMS)
Let's dive into the details of our latest features!
🛒 Pick to Tote [Beta Release] — E-commerce Picking Workflow
We are very excited to announce the Beta release of Pick to Tote! If you would like to join the Beta Release User Group to begin using Pick to Tote in Beta today, you can request access here.
A key component of e-commerce fulfilment is the ability to pick large numbers of small orders quickly and efficiently. Pick to Tote is designed to do just that, streamlining the picking process for warehouses handling large numbers of small orders.
What is Pick to Tote in E-commerce?
Pick to Tote is a workflow in which warehouse pickers push trolleys fitted with multiple totes (buckets) through the warehouse. Each tote corresponds to an individual order, allowing workers to pick items for several orders simultaneously. This method is ideal for small orders (typically fewer than 5 items), enabling the picking of 10 to 30 orders in one trip, dramatically saving on walking distance and time.
Here’s why Pick to Tote is a game changer:
- Improve Accuracy: By assigning items directly to their respective totes as soon as they are picked, Pick to Tote reduces the risk of mixing products between orders. This ensures that each tote contains only the items for its designated order, improving overall pick accuracy.
- Increase Speed: The ability to pick multiple orders in one trip significantly reduces walking time through the warehouse, eliminating the need for retracing steps or making multiple trips. This streamlined process increases the speed of order fulfilment and optimises warehouse operations.
Once picking is complete, the trolley is wheeled to the packing station, where the Pack Screen is used to finalise and pack each order into its respective shipper(s). This combination of Pick to Tote and our new Pack Screen [coming in Q1 2025] offers an efficient, end-to-end solution for e-commerce fulfilment, allowing warehouses to handle high order volumes with greater speed and accuracy. Note: Pick to Tote is currently in Beta and needs to be enabled within your CartonCloud account by one of our team. If you would like to begin using Pick to Tote in Beta, you can reach out to our team to request access today!
For more information on Pick to Tote, see our:
- Video guide below, showing how to use Pick to Tote
- Beta User Guide, which details how to setup and configure pick to tote as well as the known limitations of the Beta release.
🤳 Wave Pick Templates – Streamline Your Picking Operations!
We’re thrilled to introduce Wave Pick Templates, a powerful new feature designed to save time and optimise your warehouse picking operations.

You can now create & save your most frequently run Wave Pick configurations and reuse them whenever required. By utilising predefined templates, you can ensure that every shift and team follows the same processes, improving consistency and reducing errors in your warehouse. Templates turn what used to be a time-consuming task into something that can be done in seconds, allowing you to focus on more important tasks.
This functionality can be used in conjunction with Wave Pick Auto Generation (below) to reduce/remove the need to manually create Wave Picks.
For more information see our CartonCloud Help Wave Pick Templates page.
Wave Pick Auto Generation [Beta] *for WMS Premium Customers
For our WMS Premium customers, we have also released the Beta version of Wave Pick Auto Generation that will further enhance your picking operations.
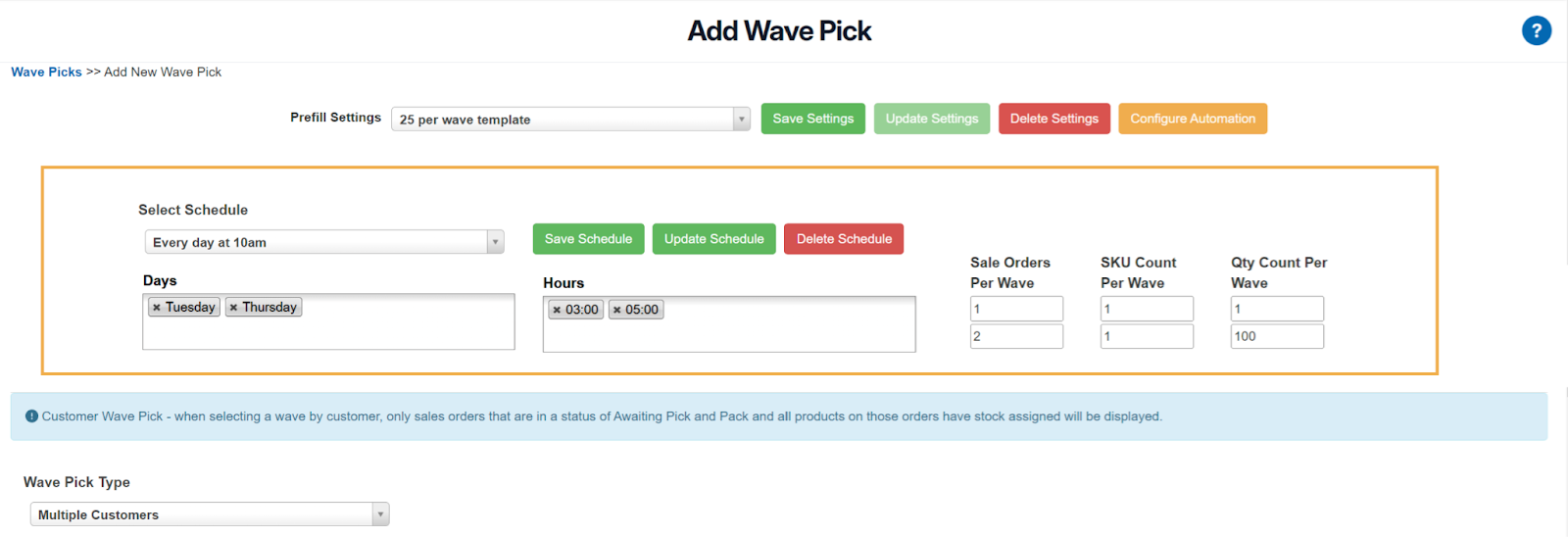
Wave Pick Auto Generation allows scheduling Wave Pick templates to generate automatically, with rules around min/max number of orders, SKU counts, total quantities, and specific days of the week and times.
Want to join our Beta User Group today? During the Beta release of this feature, customers will need to reach out to our team to have the Automation turned on and scheduled for them. You can send a request to our support team and one of our friendly team members will work with you to get this set up. Stay tuned, the ability to configure Auto Generation yourself is coming in November!
For more information refer to our Release Log Article here.
📸 Photos & Documents on Purchase Orders – New Improvements!
Our October updates make it easier to create and manage purchase order documents, from adding documents directly in the mobile app to capturing photos and videos at the product level. (See more in our Product Spotlight on Photos and Documents on POs.)
Document Creation from Product View
One of our standout updates is the ability to create documents seamlessly while viewing specific purchase order products in the mobile app, making it faster and easier to record damage information about specific items.
You are able to capture both photos and videos while editing a purchase order product and to assist in identification, the Product Code and Product Name will be automatically filled into the document description. If the status of a product is changed to Damaged, we will also ask whether a damages document needs to be created for that product.
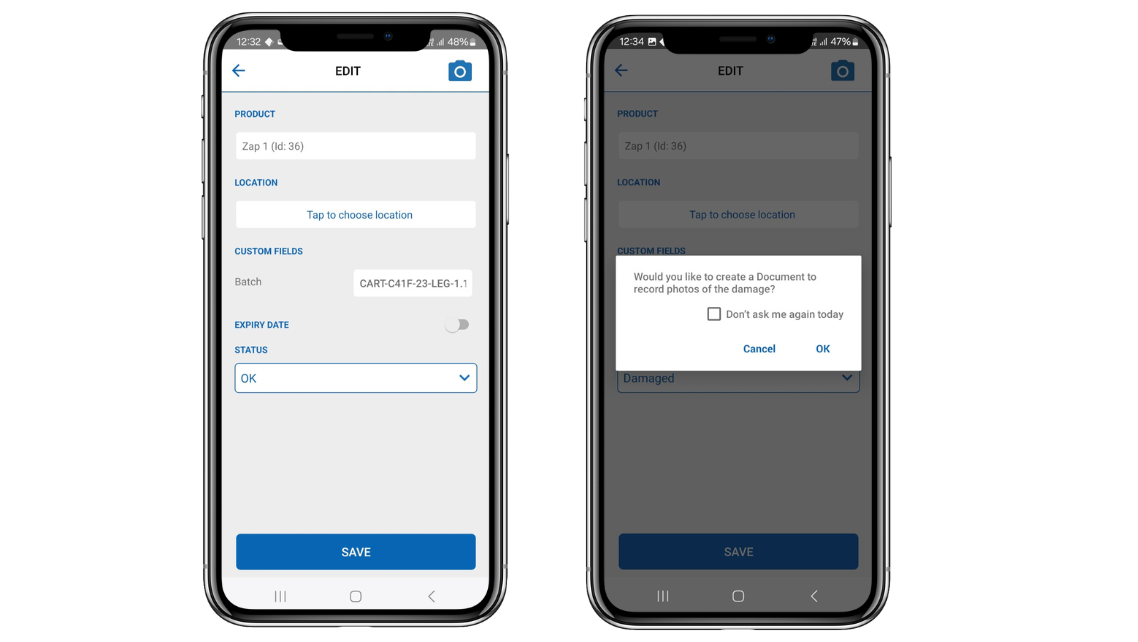
New Photos on Inbound Video Capabilities
Say goodbye to static photo limitations! We’ve added video recording support to take your documentation to the next level. Some scenarios require more than just a snapshot. Now you can record videos to capture intricate details, providing more comprehensive documentation.
We have also included Smart Audio Controls when using the new video functionality. Our smart audio feature ensures videos are silent (no audio recorded) by default, which is particularly useful in noisy warehouse environments. While filming, an easy-to-use microphone toggle lets you add voice notes if needed.
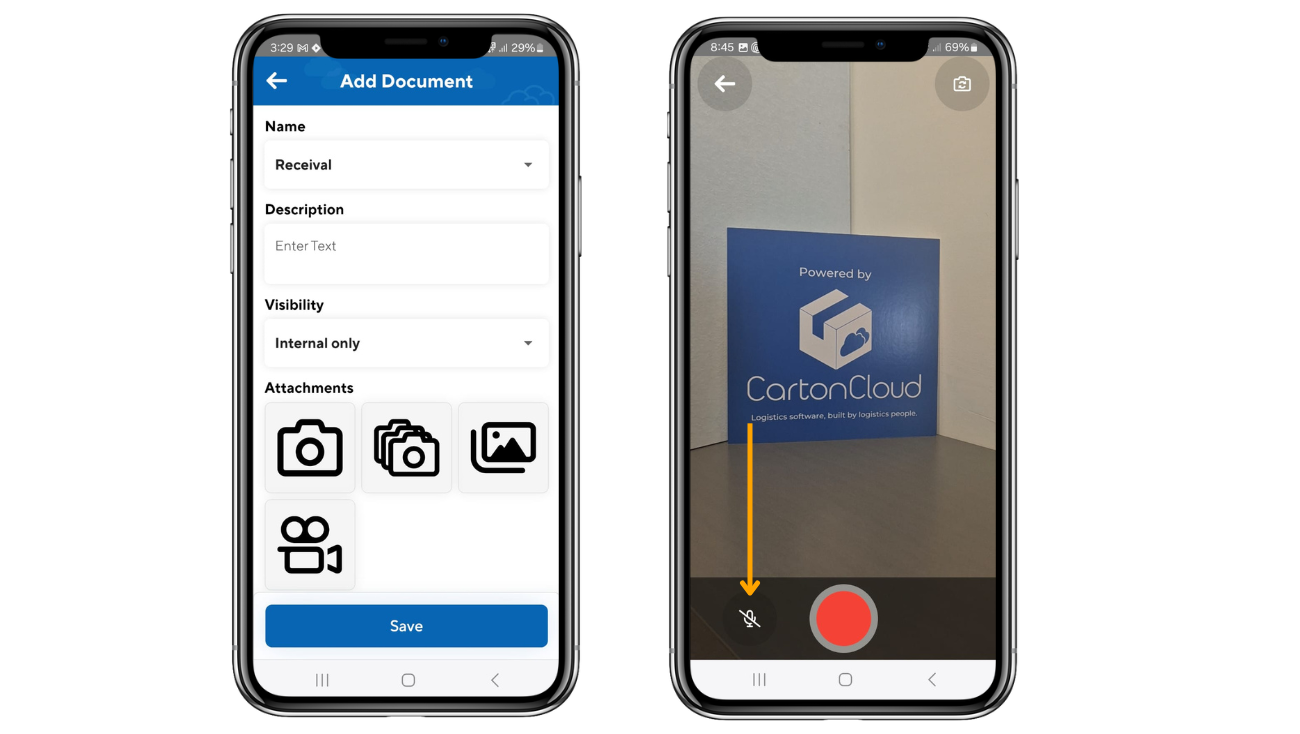
New Photo and Video Lightbox Feature
Managing photos has never been easier! The new lightbox feature enhances your experience with document images and videos on the webapp. You can now more easily view, scroll through, and download photos or videos directly from the Document Edit screen on the web app. All images are displayed clearly within the lightbox, allowing you to stay on the same page while accessing them.
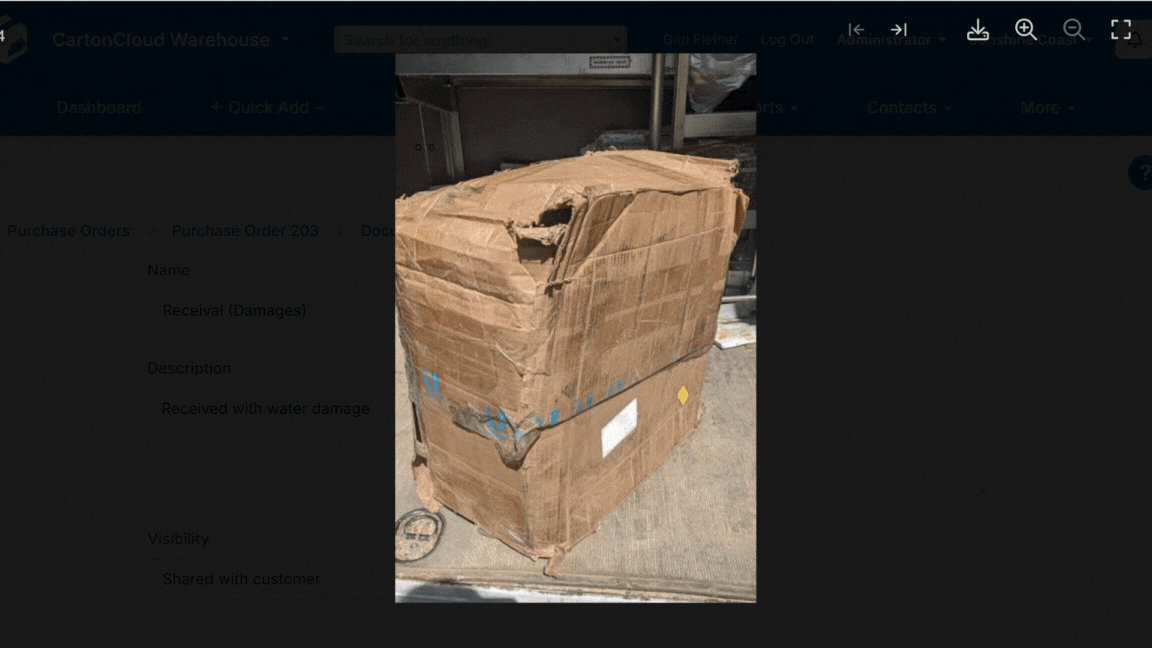
Grid View Layout Option
You can now customise how you view your Photos and Documents captured on Purchase Orders with our new grid view layout. Depending on your preference, you can choose between a traditional list view or an image-rich grid view to better manage your documents. Whether you prefer a cleaner, detailed list or a grid-based layout, this option allows you to work the way that suits you best.
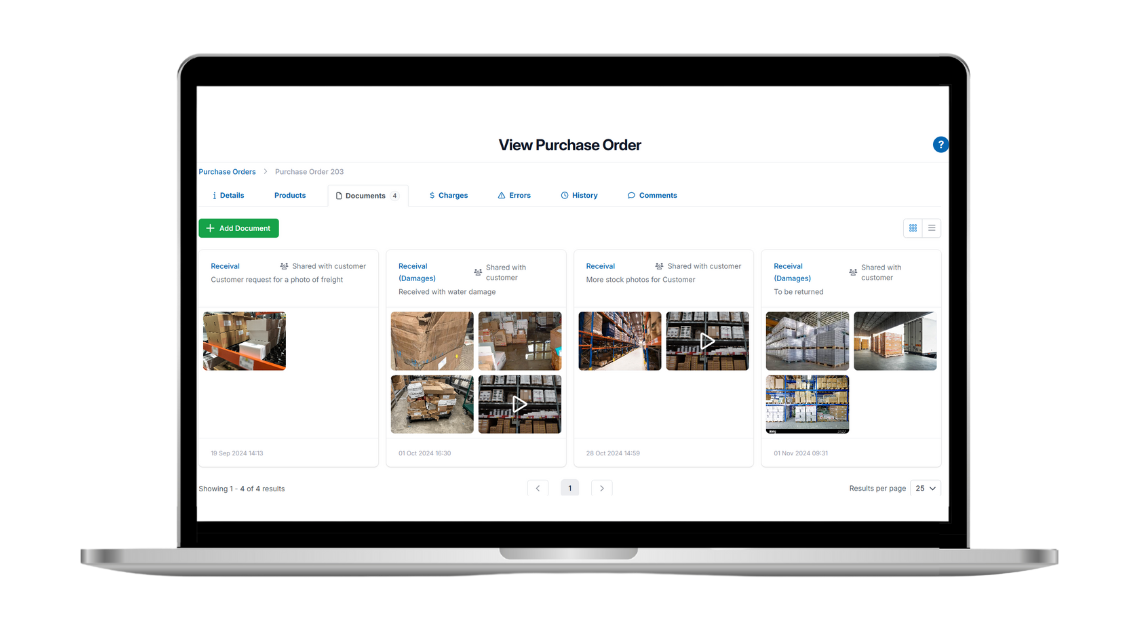
🎓Access quick learning resources in CartonCloud Academy
Become certified in our new feature - Photos and Documents on Purchase Orders through the CartonCloud Academy. Ensure your team is up to date with how to use the latest CartonCloud features. Reach out to our team here to get you and your team free access to online training via the CartonCloud Academy.
📍Editing & Emptying Warehouse Locations
We’ve made it easier to manage your warehouse locations in CartonCloud with direct editing capabilities. You can now update allowed product types and adjust location capacity without downtime, even for occupied spaces.
Edit Product Types Directly
You can now modify Product Types directly from the Warehouse Location edit page! You can update the product types assigned to any warehouse location without needing to navigate away from the Warehouse Location Edit page.
Instead of jumping between pages or relying on the bulk edit page, you can now modify product types in just a few clicks. It’s a faster, more intuitive way to ensure the right products are assigned to the right locations.
Update Location Capacity
Managing pallet locations is easier with new capacity adjustment capabilities. You can now Adjust Capacity for Single or Multiple Pallet Locations, all from the Edit Warehouse Location page.
By simplifying the process of updating location capacity, you can make real-time adjustments to optimise space usage within your warehouse. Whether it’s reallocating space for incoming stock or fine-tuning the capacity for specific locations, this update gives you more agility in managing your storage.
Update Location Capacity without emptying the location
The ability to adjust warehouse capacity without operational downtime is a game-changer for warehouse managers. It allows you to respond to changing demands or optimise space usage without halting other processes, keeping your warehouse running efficiently at all times. You can now switch a location from being Multi Pallet to Single Pallet (or vice versa), without first emptying the location.
For more information on how to update warehouse locations, visit our CartonCloud Help Guide for Warehouse Locations.
🙋🏽Have Your Say! We want your feedback
At CartonCloud, we’re constantly working to enhance your experience, and your feedback is essential in helping us shape future improvements. We’d love to hear from you!
How You Can Help:
- Take a quick survey and share your thoughts on our recent features
- Help us drive future updates that matter most to you
- Plus, you’ll be entered to win a $250 Amazon Gift Card!
- Take the Survey Now!
🚀 Explore New Features Coming Soon!
Mobile-based Wave Pick Generation
Expected Release: December 2024
We are excited to announce the upcoming Mobile-based Wave Pick Generation feature, designed to significantly accelerate the creation of wave picks and streamline warehouse operations while on the move.
Mobile app users will be able to select from their preconfigured Wave Pick Templates and generate Wave Picks directly from the mobile app.
Photos & Documents on Sale Orders
Expected release: January 2025
We're extending our Photos & Documents functionality to Sale Orders! This means users will have the same streamlined experience and powerful tools they’re familiar with on Purchase Orders now available when processing Sale Orders.
With this enhancement, users packing sale orders on the mobile app can easily capture photos, upload documents, and attach these directly to the Sale Order. Whether you need to share these documents with customers to keep them informed or manage them internally for smoother warehouse operations, this feature will add a new level of flexibility and transparency to your order processing.
Stay tuned for more details on this update, designed to make managing and sharing order information easier than ever!
Replenishment Auto Generation
Expected release: December 2024
Building on our Wave Pick Auto Generation (expected to release in November), we’ll be rolling out Auto Generation for Replenishments. This will eliminate any time taken to setup and create replenishments as they can be scheduled to create automatically in the background.
Replenishment Auto Generation will require Advanced Automation which is part of Warehouse Premium.
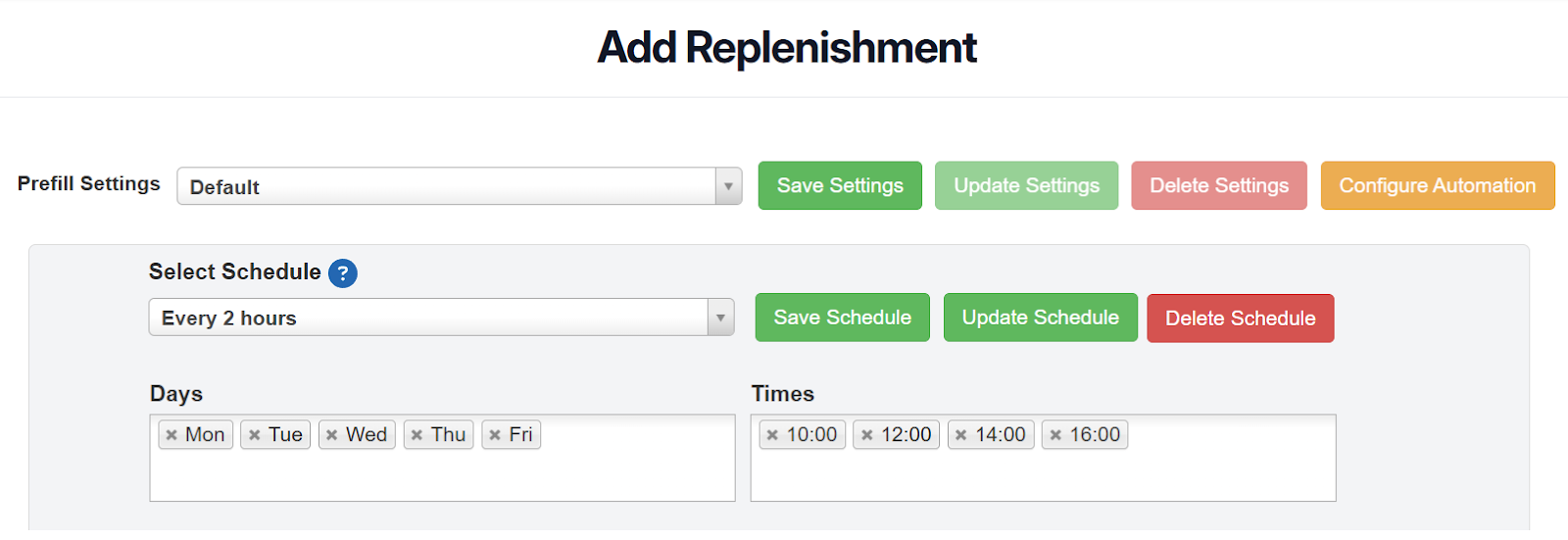
Pack Screen
Expected release: April-June 2025
We’re excited to introduce our upcoming Pack Screen feature, designed specifically for high-volume e-commerce and B2C environments. This streamlined interface supports separate picking and packing workflows, making the process faster, more accurate, and more efficient.
Key Features and Benefits:
- Split Picking and Packing: The Pack Screen allows separate workflows for pickers and packers, enabling bulk picking and designated packing stations for high-volume orders.
- Enhanced Accuracy: Packers can verify items manually or with barcode scanning to ensure accuracy, reducing errors and enhancing customer satisfaction.
- Integrated Carrier Selection: Directly print shipping labels and select carriers through integrations like Starshipit, with rules-based or manual selection options for flexibility.
- Connected Scale Support: Pack Screen supports connected scales for accurate shipment weights, minimising manual errors.
- Efficiency-Focused Design: Optimised for scanning, the Pack Screen reduces physical interaction, boosting speed and efficiency in fast-paced settings.
This feature will significantly improve the packing process for high-volume warehouses, making it easier to manage large numbers of small SKU orders, ensure accuracy, and streamline shipping.
API Enhancements
Expected Release: Jan-March 2025
TMS Quotes API
Need to provide quotes to external parties and platforms?
We are excited to announce that CartonCloud users will soon have the ability to use the CartonCloud API to determine freight costs in advance of creating a consignment. This allows external parties to query for freight rates before creating a consignment.
For ease of use, the API structure will be similar to our existing Consignments API.
Consignment Update API
We’re excited to announce that a new API endpoint for updating consignments is on the way! This feature will allow developers to seamlessly update consignment details directly via the API, giving you even more control over your logistics processes.
With this new endpoint, you’ll be able to make real-time updates to key consignment data, ensuring your systems are always up-to-date and reducing manual intervention.
Stay tuned for more details on how to implement this new functionality and streamline your workflow!
Invoice API
We’re excited to announce that later this quarter, we’ll be releasing a powerful new Invoice Webhook designed to sync seamlessly with external systems! This webhook will provide all the necessary details to ensure accurate and up-to-date invoicing information across platforms.
This new webhook will simplify your integration with external systems, keeping invoice information in sync across systems. Stay tuned for the official release!
Item-Level Scanning (TMS)
Expected Release: Staged rollout throughout Jan-June 2025
Item-Level Scanning is coming to the CartonCloud Transport Management System.
Item-level scanning will allow drivers to scan individual item barcodes at the point of delivery, and allow warehouse staff (and drivers) to scan consignment items on and off vehicles when loading and unloading, providing significantly greater visibility throughout the transport process.
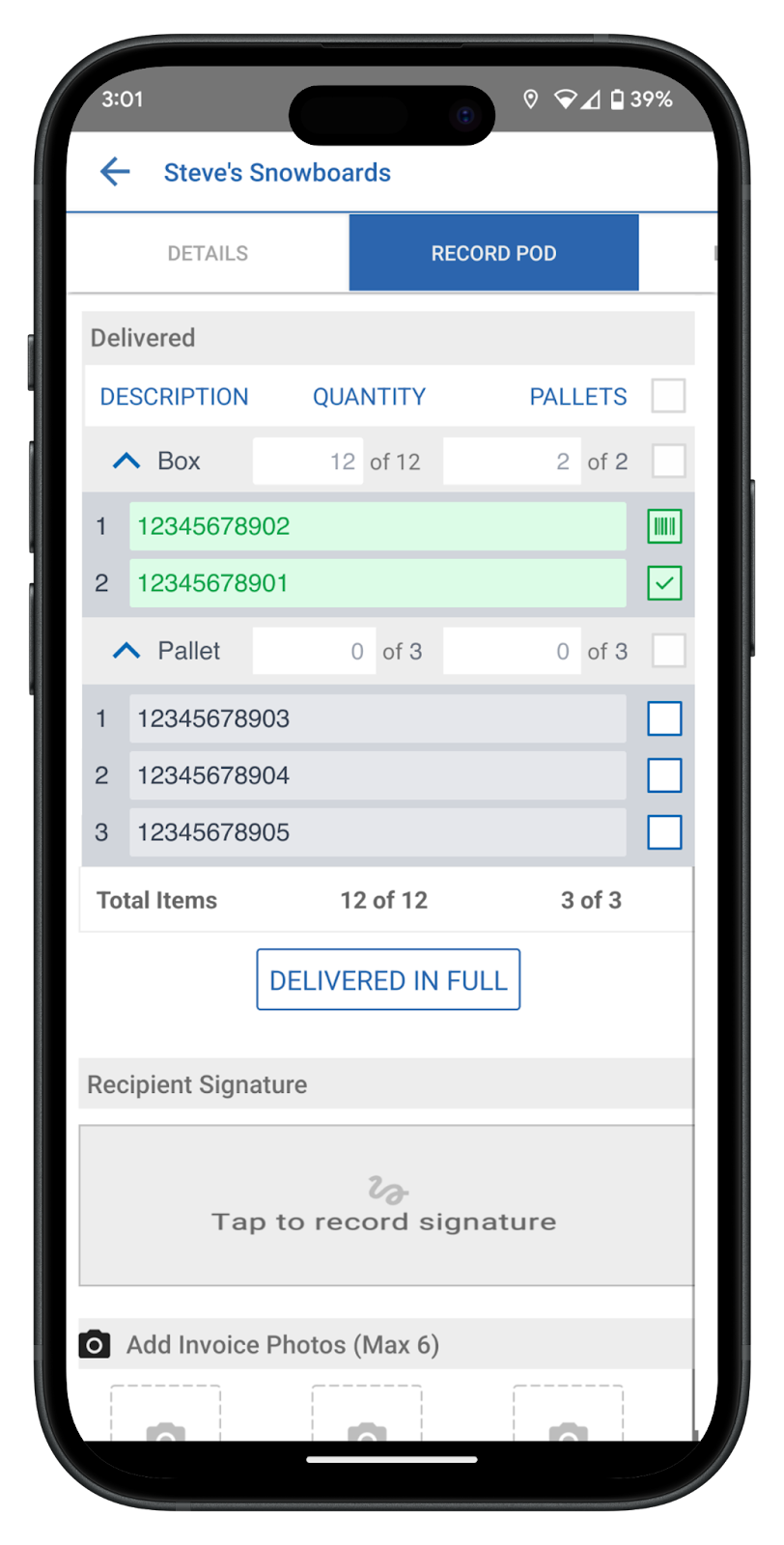
Consignment Items Screen Revamp
Expected Release: Dec 2024
As we work toward Item-Level Scanning on the TMS, we’re revamping the Consignment Items User Interface on the webapp. In addition to being able to print item-level labels, we’re also enhancing the UI to show information more clearly and avoid users needing to side-scroll when they have a large number of custom fields. This will make it considerably faster and easier to add, edit and process consignment items.
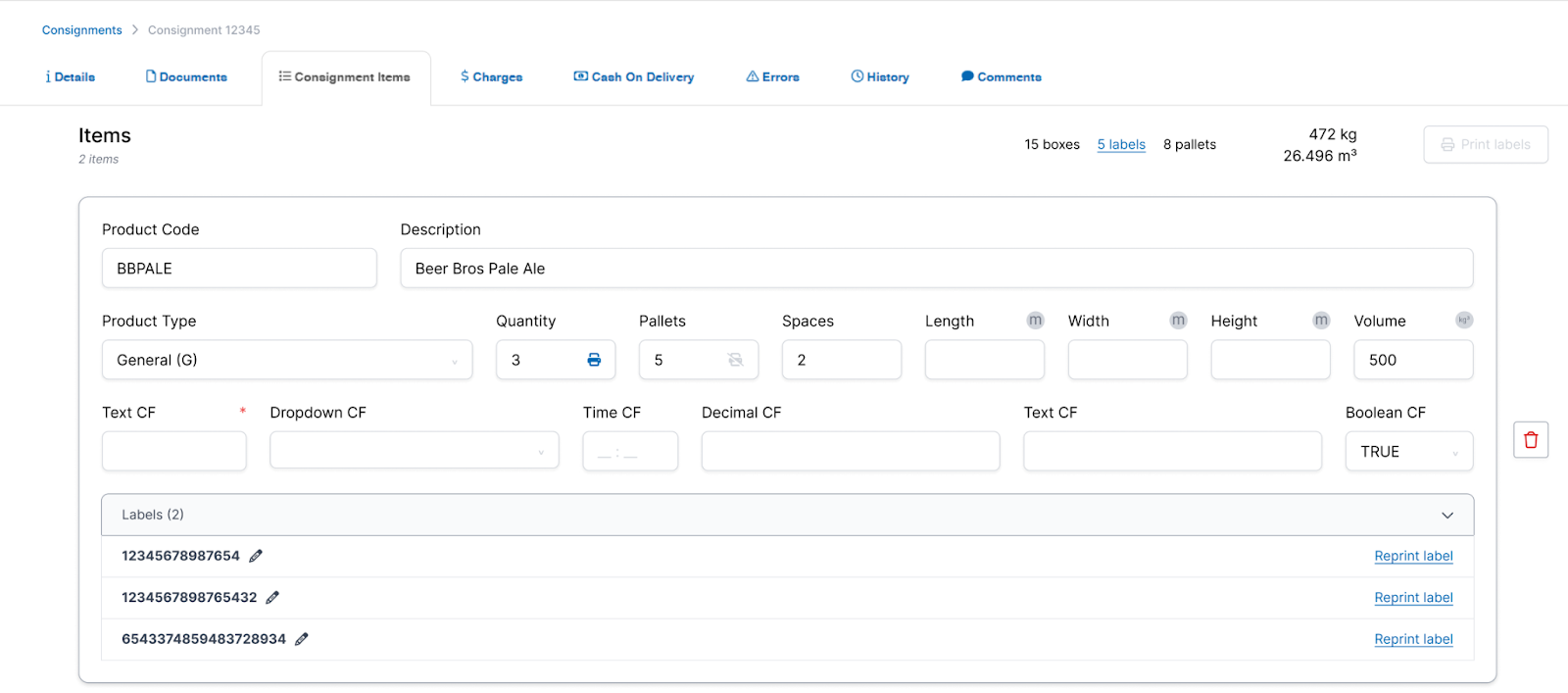
Subscribe to CartonCloud
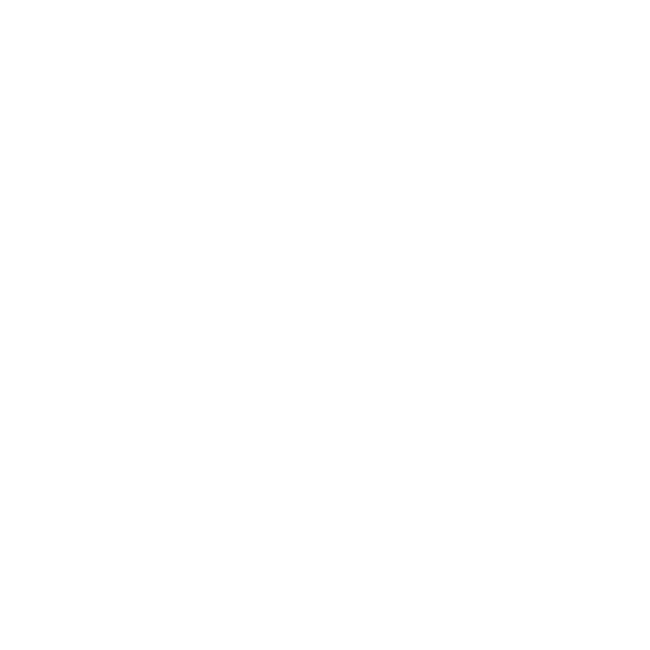